Introduction:
Work truck trailers play a vital role in various industries, from construction to agriculture, transportation, and beyond. These trailers are essential for transporting goods, equipment, and materials from one place to another efficiently. To ensure the durability and reliability of work truck trailers, welding is a crucial process that requires a combination of skill, precision, and knowledge. In this comprehensive guide, we will delve into the world of work truck trailer welding, exploring the techniques, materials, and considerations involved in creating strong and durable trailer structures.
Section 1: Understanding Work Truck Trailers
Before we delve into the intricacies of welding work truck trailers, it is essential to understand the different types of trailers commonly used in various industries. Work truck trailers can vary in size, design, and construction based on their intended use. Some of the most common types of work truck trailers include flatbed trailers, utility trailers, dump trailers, and enclosed trailers. Each type of trailer serves a specific purpose and requires different welding techniques to ensure structural integrity and longevity.
Section 2: Importance of Welding in Work Truck Trailers
Welding is a critical process in the construction of work truck trailers as it involves joining metal components together to create a strong and durable structure. Proper welding techniques ensure that the trailer can withstand heavy loads, rough terrain, and harsh environmental conditions without compromising safety or performance. Welding also plays a significant role in repairing and maintaining work truck trailers, helping to prolong their lifespan and ensure optimal functionality.
Section 3: Welding Techniques for Work Truck Trailers
Several welding techniques can be used in the construction and repair of work truck trailers, each with its own advantages and applications. Some common welding techniques used in work truck trailer welding include:
1. MIG Welding: Also known as Gas Metal Arc Welding (GMAW), MIG welding is a versatile and efficient welding process that uses a consumable wire electrode and shielding gas to create strong welds. MIG welding is commonly used in trailer construction for its speed and ease of use.
2. TIG Welding: Tungsten Inert Gas (TIG) welding is a precise welding technique that uses a non-consumable tungsten electrode and inert gas to create high-quality welds. TIG welding is often used for welding thin metal components in work truck trailers.
3. Stick Welding: Shielded Metal Arc Welding (SMAW), or stick welding, is a versatile welding process that uses a flux-coated electrode to create strong welds. Stick welding is suitable for welding thicker metal components in work truck trailers.
4. medium rescue truck -Cored Arc Welding: Flux-Cored Arc Welding (FCAW) is a semi-automatic welding process that uses a tubular wire electrode with flux inside to create strong welds. FCAW is commonly used in welding heavy-duty components in work truck trailers.
Section 4: Materials Used in Work Truck Trailer Welding
The choice of materials is crucial in work truck trailer welding as it directly impacts the strength, durability, and performance of the trailer. Common materials used in work truck trailer construction include:
1. Steel: Steel is the most commonly used material in work truck trailer construction due to its strength, durability, and affordability. Different grades of steel can be used based on the specific requirements of the trailer.
2. Aluminum: Aluminum is a lightweight and corrosion-resistant material that is commonly used in work truck trailer construction, especially for applications where weight savings are crucial.
3. Stainless Steel: Stainless steel is known for its corrosion resistance and durability, making it suitable for work truck trailers operating in harsh environments or carrying corrosive materials.
Section 5: Considerations for Work Truck Trailer Welding
When welding work truck trailers, several factors must be considered to ensure the quality and integrity of the welds. Some key considerations include:
1. Joint Design: The design of the weld joint plays a crucial role in determining the strength and durability of the weld. Proper joint design, including the type of joint and preparation of the mating surfaces, is essential for creating strong welds in work truck trailers.
2. Welding Parameters: The selection of welding parameters, such as voltage, current, travel speed, and shielding gas flow rate, is critical in achieving high-quality welds in work truck trailers. Proper adjustment of welding parameters based on the material and thickness being welded is essential for optimal results.
3. Welding Position: The welding position, whether flat, horizontal, vertical, or overhead, can significantly impact the quality and appearance of the weld. Proper positioning of the workpiece and the welder is essential to ensure consistent and uniform welds in work truck trailers.
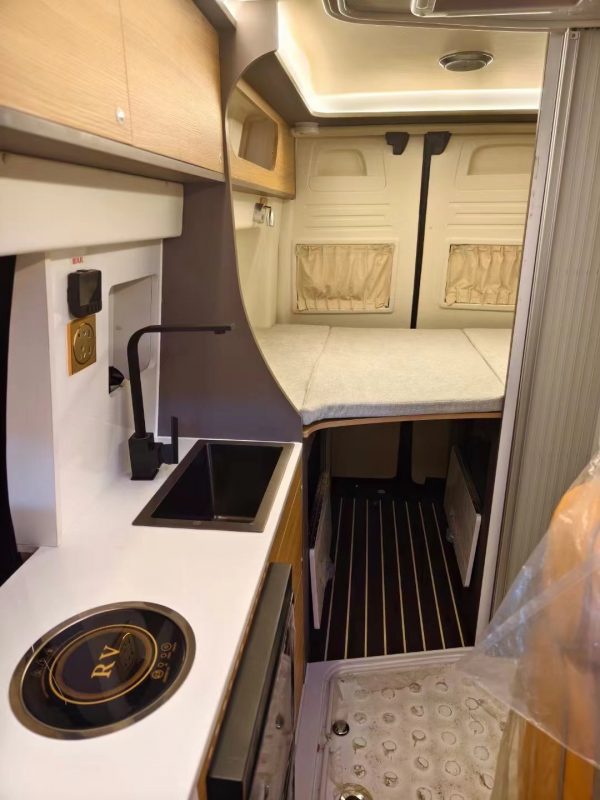
Section 6: Safety Considerations in Work Truck Trailer Welding
Safety should always be a top priority in work truck trailer welding to prevent accidents, injuries, and damage to equipment. Some essential safety considerations to keep in mind during welding operations include:
1. Personal Protective Equipment: Welders should always wear appropriate personal protective equipment, including welding helmets, gloves, aprons, and safety glasses, to protect themselves from sparks, UV radiation, and fumes.
2. Ventilation: Adequate ventilation is essential in welding environments to remove welding fumes and gases that can be harmful to health. Proper ventilation systems, such as exhaust fans or fume extractors, should be in place to ensure a safe working environment.
3. Fire Safety: Welding operations can pose a fire hazard due to sparks and heat generated during the process. Welders should have fire extinguishers, fire blankets, and other fire safety equipment readily available to respond quickly to any fire emergencies.
Section 7: Maintenance and Repair of Work Truck Trailers
Regular maintenance and timely repairs are essential to prolong the lifespan and ensure the optimal performance of work truck trailers. Some common maintenance tasks and repair techniques for work truck trailers include:
1. Inspection: Regular inspections of work truck trailers should be conducted to identify any signs of wear, damage, or corrosion that may affect the trailer's structural integrity. Inspections can help detect potential issues early and prevent costly repairs or replacements.
2. Cleaning and Lubrication: Keeping work truck trailers clean and well-lubricated can help prevent corrosion, reduce friction, and extend the lifespan of moving components such as hinges, latches, and suspension parts.
3. Welding Repairs: Welding is often used to repair work truck trailers that have suffered damage or structural failures. Welding techniques such as MIG welding, TIG welding, or stick welding can be employed to repair cracks, breaks, or other defects in the trailer structure.
Conclusion:
Work truck trailer welding is a specialized skill that requires a combination of technical expertise, precision, and practical experience. By understanding the various welding techniques, materials, considerations, and safety measures involved in work truck trailer welding, welders can create strong and durable trailer structures that meet the demands of various industries. Proper maintenance and timely repairs are essential to ensure the longevity and optimal performance of work truck trailers, making welding an indispensable process in the world of work truck trailer construction and repair.